- Recent Articles
-
Buyers Guides
- HOW TO USE COMFORT RATINGS
- BUYERS GUIDE: INSULATED WORK GLOVES
- BUYERS GUIDE: COLD WEATHER WORK BOOTS
- BUYERS GUIDE TO PAC BOOTS
- BUYERS GUIDE TO BASE LAYERS
- BUYERS GUIDE: PANTS OR BIB OVERALLS?
- BUYERS GUIDE: COVERALLS OR BIB OVERALLS?
- BUYERS GUIDE TO GLOVE DIPS & COATINGS
- LATEX vs. NITRILE COATED: WHICH IS THE RIGHT GLOVE?
- WHAT KIND OF WORK GLOVES ARE RIGHT FOR MY JOB?
- HAND PROTECTION THAT KEEPS PRODUCTIVITY HIGH
- THE IMPORTANT ROLE OF HAND PROTECTION
- VITACOMFORT: A NEW LEVEL OF COMFORT & SAFETY
- WHAT TO LOOK FOR WHEN CHOOSING A WINTER WORK COAT
- WHY IS SYNTHETIC INSULATION BETTER?
- AIRBLAZE INSULATION DELIVERS MORE WARMTH WITH LESS WEIGHT
- WARMPLUS GRAPHENE LINING MAKES WARMER WORK GEAR
- DON'T COMPROMISE PROTECTION FOR PERFORMANCE
- WHY SOFTSHELL JACKETS ARE PERFECT FOR WORKING IN THE COLD
- EMBRODIERY
- Case Studies
-
Best Practices
- NATIONAL SAFETY MONTH: HIGH-VISIBILITY WORKWEAR THAT WORKS AS HARD AS YOUR CREW
- COLD TIPS
- NEW OSHA RULE ON PPE FOR WOMEN
- HOW TO PREVENT COLD STRESS INJURIES IN ROAD CREWS
- HOW TO STAY SAFE IN CONCRETE CONSTRUCTION
- KEY TERMS & DEFINITIONS
- HOW TO USE GLOVE LINERS
- THE IMPORTANT ROLE OF HAND PROTECTION
- PROPER FOOT CARE FOR WORKING IN THE COLD
- HOW TO PREVENT SLIPS, TRIPS & FALLS
- HOW TO CHOOSE HIGH-VISIBILITY WORKWEAR
- HOW TO LAYER WITHOUT OVERHEATING
- HOW OVERDRESSING HURTS PRODUCTIVITY
- HOW TO DRESS FOR WORKING IN THE COLD
- SAFETY TIPS FOR WORKING IN THE RAIN
- HOW TO DRESS FOR WORKING IN DIFFERENT TEMPERATURES
- HOW TO STAY SAFE & WARM WHILE WORKING OUTSIDE IN THE WINTER
- HOW TO SAFELY MANAGE & PREVENT COLD STRESS
- HOW TO STAY WARM WORKING WITH PRODUCE
- PREPARING FOR TEMPERATURE SWINGS
- THE SCIENCE OF STAYING WARM
- HOODS OR HATS: WHICH ONE IS SAFER?
- HOW DRIVERS & TRANSPORTATION WORKERS STAY DRY
- PERSONAL PROTECTIVE GEAR EVERY DRIVER NEEDS
- CHALLENGES OF WORKING IN LOW TEMPERATURES AS A DRIVER
- PROTECT YOUR TRUCK DRIVERS WITH HIGH-VISIBILITY WORKWEAR
-
Industry Knowledge
- TRADESHOWS & EVENTS
- KEY TERMS & DEFINITIONS
- KEY TERMS & DEFINITIONS
- BEST CLOTHING FOR MAINTENANCE STAFF IN FOOD PROCESSING
- HOW DO I STAY WARM WHILE WORKING IN MEAT PROCESSING?
- HOW TO STAY WARM IN A COLD STORAGE FREEZER
- 5 IMPORTANT PIECES OF CLOTHING FOR COLD STORAGE WORKERS
- GEAR THAT DRIVES PEAK PRODUCTION AS A FORKLIFT DRIVER
- CHALLENGES OF WORKING IN LOW-TEMPERATURE INDOOR ENVIRONMENTS
- PROTECTING PERISHABLES IN FOODSERVICE DISTRIBUTION
- TEMPERATURE CONTROL UNDER FSMA
- BEST HIGH-VISIBILITY JACKETS FOR CONSTRUCTION WORKERS
- COLD WEATHER SAFETY CHECKLIST FOR CONSTRUCTION WORKERS
- TOWER CLIMBER'S GUIDE TO WORKING OUTSIDE IN WINTER
- UTILITY WORKER'S GUIDE TO KEEPING WARM IN WINTER
- HOW TO IMPROVE DRIVER RETENTION AND RECRUITING
- THE IMPACT OF PROPER ERGONOMICS ON DRIVER WELLNESS
- QUALITY WON'T BE COMPROMISED
- WHY IRON-TUFF IS THE MOST ICONIC COLD WEATHER CLOTHING
- WHY ALL WORKERS NEED HIGH-VISIBILITY WORKWEAR
- HOW TO STAY SAFE IN LOW VISIBILITY & HIGH TRAFFIC CONDITIONS
- THE REAL COST OF HIGH EMPLOYEE TURNOVER
- HOW DOES PPE AFFECT YOUR BOTTOM LINE?
- MEDICAL COSTS OF PREVENTABLE INJURIES
- HOW TO STAY SAFE IN CONCRETE CONSTRUCTION
- HOW TO IMPROVE EMPLOYEE RETENTION IN COLD STORAGE
- HOW TO PREVENT COLD STRESS INJURIES IN ROAD CREWS
- HOW TO CHOOSE COLD WEATHER WORKWEAR FOR ROOFERS
- Use & Care
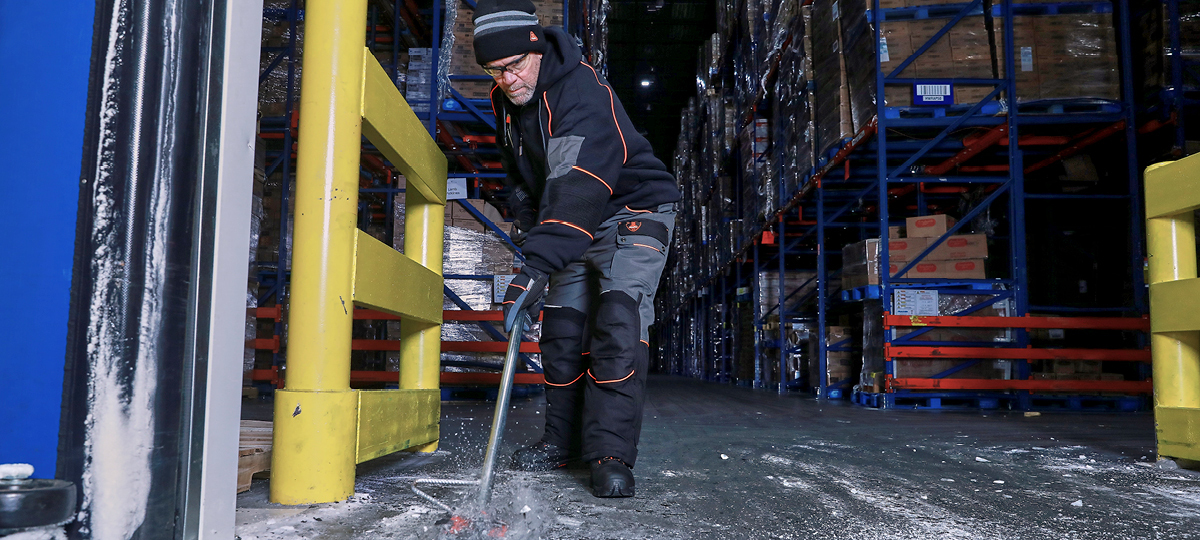
BOOSTING EMPLOYEE RETENTION IN COLD STORAGE THROUGH HEALTH AND SAFETY INITIATIVES
Working long hours in cold storage is not for the weak. Because of this, employee retention can be challenging to uphold. With frequent safety training sessions and competitive health benefits, facilities could begin seeing lower turnover rates within their workplaces.
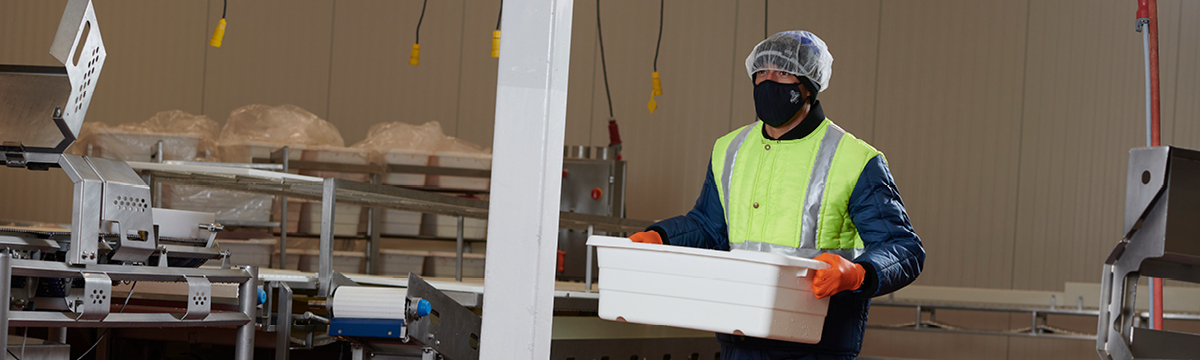
Creating a Safety Culture
There is a misconception amongst organizations who think that “employee trainings are costly, time-consuming, and only necessary for new hires,” says Nate Walts, CEO of WorkForge who contributed to the article Employee Health & Safety in Cold Food Facilities in Refrigerated and Frozen Foods Magazine. That is far from true. Short and easily digestible training sessions have proven to stay top of mind with employees especially when they are broken down by specific tasks or job hazards. OSHA states that the workplace should be "free of recognized hazards, including cold stress” and therefore employees should be trained “on preventing and recognizing cold stress illnesses and injuries.” Lack of training amongst employees leads to lost productivity, uncertainty on the job and worse, work-related accidents that can be costly to both the employee and the employer.
As a new hire in cold storage or food production, you can easily underestimate the quick and forceful impact working extended periods of time in frigid cold can have on the mind and body. Being educated on what you need to wear and understanding that your everyday, store-bought coat just isn’t going to keep you safe enough or warm enough in a fast-paced, dimly lit freezer environment. This can make all the difference in keeping you on the right side of a workman’s comp case.
Spotting and Preventing Cold Stress in Cold Storage
Leigh Stadelmeier, Authorized, OSHA Outreach Trainer and Vice President of B2B Outdoor Sales for RefrigiWear says workers “underestimate how exposure to relentless cold will make their bodies feel clumsy and dull their reaction times.” There are even more early signs individuals can experience when cold stress starts setting in. Teaching employees to spot the signs before consequences like hypothermia, frostbite and trench foot set in could save your business an average of $40,000 on a workplace injury case according to the National Safety Council. The signs to be aware of are:
- Shivering
- Fatigue
- Drowsiness
- Disorientation
- Cold, tingling, stinging or aching in areas followed by numbness
- Skin color turning from red to purple to white or pale in color
One of the greatest measures a cold food facility can take to prevent cold-related injuries is outfitting their workers with insulated gear that will keep them protected in the temperature-controlled areas of the facility they work in. That is one advantage that cold storage warehouses have over companies who have people working outdoors in unpredictable weather conditions – control over temperature and wind chill expectations based on job type.
Gear for Cold Storage & Food Processing
Below Freezing Gear:
Subzero Gear:
Gear for Forklift Drivers:
Gear for Food Processors:
High-Visibility Gear:
Employee Retention & Other Benefits
When employees sign on to work in cold food facilities, they understand their assignments can have them facing long exposure to cold that is not without its risks. But the wear and tear this can have on a person is what eventually causes high turnover in this industry. That doesn’t mean that major cold storage companies aren’t looking for ways to implement new design features which reduce employee's exposure to cold and minimize physical strain on workers bodies. To enhance both safety, efficiency and employee well-being companies are actively incorporating more automated systems into their processes. To further reduce employee turnover some companies have launched on-site health centers in their facilities to offer a range of services to insured workers from primary care to chronic condition management at no cost to employees and their families.
The cold storage industry faces unique challenges in maintaining employee health and retention, given the demanding work conditions. Training employees on cold stress, equipping them with proper gear, and improving facility design can reduce injury risks and enhance safety. Organizations investing in regular safety training and competitive health benefits, such as on-site health centers and task-specific training, are seeing improvements in workforce stability. By prioritizing employee health and cold-preparedness, companies can better support their teams and reduce costly turnover in these challenging roles.